
The next step is the worst part (imho) and that’s crimping header connectors onto 25 wires. First step was to get a couple of Ardunio. This thread will document the process of getting grbl to drive the Gecko G540 controller. However, I can’t access all the goodies that Easel provides unless I run grbl. It works well and I’ve been successfully creating gcode using (mostly) CamBam.
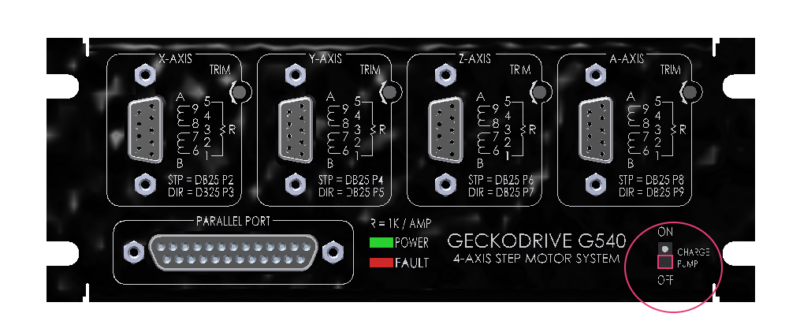
No power supply required and no fan, the G540 is in a separate, cooled enclosure I’ve mentioned in previous posts, that I run my X-Carve under Linuxcnc with a Gecko G540 controller. This combination of Arduino and cncshield will go in a small plastic box with a USB socket in one end and the DB25 cable at the other. gecko g540 wiring diagram for mach 3 thank you for visiting our site this is images about gecko g540 wiring.
#Gecko g540 schematic drivers#
This shield supports 4 x 8825 stepper drivers so each Y axis motor has it’s own driver I won’t be using any of these, I’ll just be using the cncshield as a way to interface the signals via DB25 cable from the G540 to grbl. The Gecko is plug and play, you just have to put a resistance into the db9 connector if you are using motors below 3.5A (See user manual). Gecko G540 Wiring Diagram Graphics (Fastest Way to Build/Service Your System). Next I need a way to get the various control signals (XYZ step/direction, limit/home switches etc) from grbl to/from the Gecko. GECKO G540 DIY Labeling Kit (No More Headaches Wiring Or Servicing)). This thread will document the process of getting grbl to drive the Gecko G540 controller.įirst step was to get a couple of Ardunio Unos (if there are two Uno, does that make it a Due? ) They arrived from China today $A16 for both,Īs I’ve never run grbl before and all I know about it is from reading posts in this forum, a bit of reading was needed to get downloading the source code,compiling and installing on the Uno, A terminal program lets me run a $$ command and get a readable (if not yet understandable) response. So when you search the web, you will find these diagrams with north pole with This is a datasheet of a Nema 17, 6-wire, which can be connected as bipolar or as. The Gecko G540 is packed with features that make it the choice for small to medium sized CNC machines. However, I can’t access all the goodies that Easel provides unless I run grbl. Nema 17 Stepper Motor Wiring Diagram Most of the up-to-date stepper motors that I have are with eight windings. The Gecko G540 can control up to 2 relays using pins 5 and/or 6 as well as pin 12 being the GRND. I have reviewed the Gecko wiring schematics but i cant figure out one thing. In your CNC program set the axis being adjusted to move at 2 revolutions per second and use a screwdriver to turn the trimpot in the ADJUST hole on the top of the drive. Im in the process of hooking up my relays for the spindle off/on and the coolant off/on. It works well and I’ve been successfully creating gcode using (mostly) CamBam. The G540 is composed of four individual G250 motor controls, each of which has a designated pin outputting the smoothness adjust trimpot to the G540 motherboard.

I’ve mentioned in previous posts, that I run my X-Carve under Linuxcnc with a Gecko G540 controller.
